Introduction to Industrial Hygiene
Industrial Hygiene is the science dedicated to protecting and enhancing the health and safety of workers by controlling environmental factors that may lead to injury or illness. It involves anticipating, recognizing, evaluating, and implementing controls for potential workplace hazards. With a comprehensive industrial hygiene plan, businesses can reduce the risk of occupational illnesses and maintain a safe working environment.
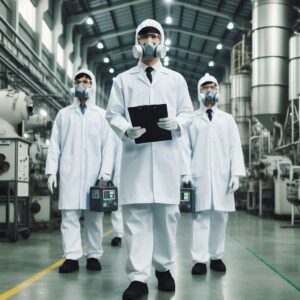
Hygiene – Definition and History
Hygiene, in general, refers to practices that promote health and prevent disease. In the workplace, industrial hygiene focuses on controlling environmental stressors that may harm workers. The concept dates back to ancient times when the Greek physician Hippocrates observed lead toxicity in miners. The modern field of industrial hygiene developed alongside industrialization in the 20th century, leading to the establishment of regulations such as the Occupational Safety and Health Act of 1970.
Industrial Hygiene Functions
The primary functions of industrial hygiene include:
- Anticipation of hazards: Predicting potential health risks based on workplace activities and materials.
- Recognition of hazards: Identifying risks such as chemicals, noise, or biological agents that may exist in the workplace.
- Evaluation of hazards: Assessing the level of exposure using scientific methods and tools like air sampling or noise meters.
- Control of hazards: Implementing control strategies using the hierarchy of control, such as elimination, substitution, engineering controls, administrative measures, and personal protective equipment (PPE).
Health Map
A health map is a tool used in industrial hygiene to document and evaluate health risks in the workplace. It helps in identifying areas of concern, mapping out exposure levels, and tracking the effectiveness of control measures over time.
Controlling Risk – Hierarchy of Control
The hierarchy of control is a widely recognized approach in industrial hygiene for managing workplace risks, arranged from most effective to least effective:
- Elimination: Completely remove the hazard from the workplace.
- Substitution: Replace hazardous materials or processes with safer alternatives.
- Engineering Controls: Using physical means, such as ventilation systems, to isolate workers from hazards.
- Administrative Controls: Implementing policies, training, and work practices to reduce exposure.
- Personal Protective Equipment (PPE): Equipping workers with safety gear, such as respirators or gloves, to protect against hazards.
Prevention or Early Warning of Ill Health
Industrial hygiene emphasizes early detection and prevention of health risks through:
- Health surveillance: Regular medical checks to detect any signs of occupational illness.
- Real-time monitoring systems: Tools like gas detectors or noise monitors that can alert workers to dangerous exposure levels.
- Worker education and training: Ensuring employees understand the hazards they may face and how to mitigate them.
Points to Consider Prior to an Industrial Hygiene Plan
Before developing an industrial hygiene plan, it’s essential to consider the following:
- Workplace hazard assessment: Conduct a thorough evaluation to identify all potential risks.
- Regulatory requirements: Ensure the plan complies with relevant health and safety regulations.
- Employee involvement: Engage workers in identifying hazards and implementing control measures.
- Monitoring and updates: Continuously evaluate the effectiveness of the plan and make necessary updates.
Types of Health Hazards in Industrial Hygiene
In industrial hygiene, workplace health hazards are classified into the following categories:
Physical Hazards
- Noise: Prolonged exposure to excessive noise can cause hearing loss.
- Vibration: Prolonged exposure to vibration can cause musculoskeletal disorders.
- Radiation: Both ionizing and non-ionizing radiation pose health risks, including cancer.
Chemical Hazards
- Toxic chemicals: Exposure to harmful substances such as solvents, fumes, or dust can result in chronic or acute illnesses.
- Respiratory hazards: Chemicals that affect the respiratory system can lead to conditions like asthma or bronchitis.
Biological Hazards
- Infectious agents: Workers may be exposed to bacteria, viruses, and fungi that can cause serious diseases or infections.
Psychological Hazards
- Workplace stress: Factors like high workloads, poor management, or workplace violence can contribute to mental health issues such as anxiety or depression.
Ergonomic Hazards
- Repetitive strain: Repetitive tasks or awkward postures can result in musculoskeletal injuries.
- Manual handling: Improper lifting techniques can lead to back and joint problems.
Occupational Exposure Assessment Strategy
A critical element of industrial hygiene is evaluating workers’ exposure to various hazards. An effective occupational exposure assessment strategy includes:
- Identifying exposure sources: Determining where and how hazards originate.
- Measuring exposure levels: Using tools like air sampling devices or noise monitors to quantify exposure.
- Comparing to standards: Ensuring exposure levels remain within permissible limits set by health and safety regulations.
- Applying controls: Implementing controls to reduce workers’ exposure.
Work Environment and Indoor Air Quality Monitoring
Maintaining a healthy work environment is central to industrial hygiene, and indoor air quality monitoring is a key practice. It involves testing for:
- Volatile organic compounds (VOCs)
- Particulate matter (dust, asbestos)
- Gases such as carbon monoxide (CO) or ozone
Regular monitoring helps detect poor air quality and enables corrective actions, such as improving ventilation.
Ergonomic Risks and Hazards
Ergonomic risks in the workplace can lead to serious health issues if not addressed. These include:
- Repetitive motions: Tasks involving repetitive movements can cause strain injuries.
- Improper workstation design: Poorly designed workstations may lead to posture problems, causing long-term musculoskeletal injuries.
Employers can mitigate ergonomic risks through proper workstation design, adjustable seating, and ensuring that tasks are physically manageable for workers.
Individuals Working in Shifts
Shift workers, especially those working at night, face unique challenges in industrial hygiene. The disruption of natural sleep patterns can result in:
- Sleep disorders
- Increased risk of cardiovascular diseases
- Mental health problems like stress and fatigue
Effective measures for shift workers include providing adequate rest breaks, optimizing lighting, and offering support for sleep management.
Toxicology
Toxicology, The study of how chemicals impact human health, serving as a key aspect of industrial hygiene. Understanding toxicological principles helps evaluate the risks posed by hazardous substances and determine safe exposure levels. Key aspects of toxicology include:
- Dose-response relationships: Assessing how different exposure levels affect health outcomes.
- Routes of exposure: Hazardous substances can enter the body through inhalation, skin contact, or ingestion.
- Acute vs. chronic exposure: Understanding the difference between short-term high-dose exposure and long-term low-dose exposure.
Conclusion
Industrial hygiene is essential for safeguarding workers from occupational health hazards. By identifying risks, assessing exposures, and implementing control measures, businesses can create a healthier, safer workplace. A proactive industrial hygiene program helps prevent illness, enhances worker productivity, and ensures compliance with safety regulations.
Pingback: Root Cause of Climate Change: Overpopulation